ºÎ½ºÅÍ ÆßÇÁ(Booster pump)¶õ?
DCS, PLC, PC, or PAS?
Unsure about blurring control system distinctions, users identify
with functionality Control Magazine - July
2001 Bob Waterbury, Senior Editor
Outside of a child's book of fiction, if you read about
converging parallel lines you might be justifiably concerned that the world as
we know it is about to end. But once parallel, now converging, control
technologies are an important trend, and without cataclysmic results.
In
fact, some control industry experts see technological convergence as an
opportunity whose time has come. Larry O'Brien, senior analyst, ARC Advisory
Group, Dedham, Mass., uses the generic term process automation system (PAS) to
describe all forms of DCS, mini-DCS, and hybrid controls (Figure 1). He
estimates the worldwide PAS market will grow to more than $9.5 billion in 2005,
up from $7.8 billion in 2000 (Figure 2).
One of the issues obscured by
this estimate is that unit cost is declining while functional capability is
increasing. At the same time, overall hardware sales are actually falling, being
supplanted by rises in software and services. Greater functionality at lower
cost means more power for the dollar.
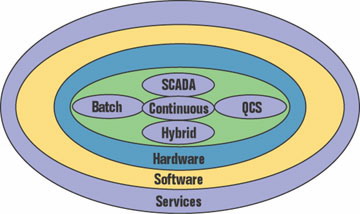 Figure 1: In ARC's
definition, the process automation system implements a selection of traditional
control system functions through a combination of hardware, software, and
services.
A more important immediate observation, however, is that the
practical and technological boundaries between a distributed control system
(DCS), programmable logic control (PLC), and personal computer (PC) control are
blurring. Units traditionally associated with process control are being used in
discrete applications. Likewise, traditionally discrete solutions are used
increasingly in both batch and continuous process control.
"That's
because a look at the underlying technology of today's solutions shows many
similarities," says O'Brien. "Today's different types of control hardware are
constructed from many of the same standard industry components such as Intel
microprocessors. Thus, the only real differences in control systems may lie at
the software level."
O'Brien points out that process and discrete
suppliers are already encroaching on each other's territory. Increased
competition between process and discrete suppliers in the hybrid industries such
as food and beverage, pharmaceuticals, and specialty chemicals are prime
examples. In such applications, the requirements of process and discrete control
are frequently interconnected, and thus combined in the control solution. "A
prime example of a hybrid process is the brewing industry," says O'Brien, "which
incorporates sequential, batch, and continuous process control in the brewing
process, and discrete control in the bottling, packaging, and distribution
processes."
A Changing Controls Market Does technological
convergence have users a little confused? A small, informal survey of
Fisher-Rosemount DeltaV users found that, when asked to classify their control
solution, some said it was a DCS. An equal number described it as either a
mini-DCS or hybrid controller. One thought it might even be a process automation
system (PAS), although he wasn't quite sure what that term meant. But each user
knew what control functions the system performs and how it fits into his overall
control scheme.
A look at the blending of control functions among
various industries, according to ARC, shows why users and suppliers are
occasionally unsure of the form and architecture of control solutions (Figure
3). Process suppliers are entering the markets traditionally served by PLC
suppliers through the introduction of hybrid controllers. And PLC suppliers are
invading the process control markets with units that perform batch processing as
well as discrete functions. The driving force in either case is industry needs
for total solutions that not only provide control, but generate production,
quality, and maintenance information for MES, ERP, and higher-level IT
functions.
The world of process automation systems includes functions
such as SCADA, batch, hybrid, continuous, and quality control. It is implemented
through a combination of various types of hardware, software, and services.
Traditional hardware solutions include DCS, PLC, and PC control. More recently,
however, hybrid controllers have entered the market poised to capture business
in both the process and discrete industries. This clearly fits the needs of
hybrid industries such as specialty chemicals, pharmaceuticals, and food and
beverage that typically comprise a rich mixture of discrete and process
functions.
But even in the petrochemical and refining industries where
continuous processes reign, there is often a number of smaller batch and
discrete functions. In many cases these functions, along with the continuous
processes, could just as easily be handled in a unified hybrid controller
database. Ultimately, corporations could use this to structure networks and fuel
the data needed for supply chain management, MES, ERP, and IT functions.
Increasingly, manufacturing data that helps improve production
efficiency is the lifeblood of companies in highly competitive markets. Such is
the case for Equistar Chemicals, Houston. By installing MES systems in addition
to its traditional DCS controls, Equistar has created statistical tools and
algorithms for determining optimum feedstock, product run, and logistics
strategies to boost yield and cut costs, according to principal engineer Robert
Brown. Company expenditures for controls last year totaled more than $50
million, but management is confident of a one-year payback because they know
that control projects tend to be the biggest moneymakers, he says.
Furthermore, companies such as Atofina Chemicals in Philadelphia are
using data storage and applied analytical software to better understand control
parameters for quality or yield improvements. By establishing baseline data, the
company can measure system performance and fine tune its processes. Without
detailed statistical analysis, process improvements may be misguided and lead to
replacing a pump when the real problem was just a valve or a pipe.
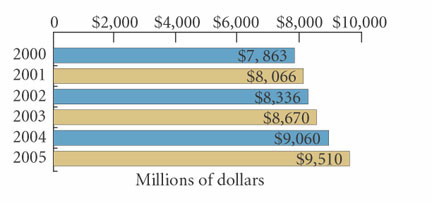 Figure 2: The process
automation system (PAS) market is predicted to grow to $9.5 billion in 2005.
(Source: ARC Advisory Group)
DCS: The Land of Giants Continuous process plants
such as refineries, petrochemicals, pulp and paper, steel mills, and textiles
still rely heavily on DCS solutions. Some are moving new applications to hybrid
controllers such as Honeywell's PlantScape or Fisher-Rosemount's DeltaV, but
large-scale legacy systems still control most of the continuous processes. Even
PLCs are not left out of the picture in large continuous process plants. They
are often used for discrete control in such functions as conveyors, motion
control, and machine control.
"DCS really grew out of the heavy process
industries," says George Dolan, a Houston-based controls engineer and consultant
with experience at Lonza Chemicals, Exxon, Nalco, Texas Instruments, STRG
Controls, and elsewhere. "But the market and the equipment have changed
considerably over the years. DCS and PLC worlds are blending as some DCS systems
are now operating on Windows NT platforms and HMI is being added to PLCs. In
fact, a PLC can do nearly everything today that a DCS can do. I know, because I
have successfully crossed that line and put a PLC with HMI in charge of a
continuous process control application. The DCS may still offer some advantages
when it comes to redundancy and hot swap capability, but new PLCs can offer that
today, too."
Dolan considers the PLC to be a less expensive solution to
a given application than DCS. However, over the lifecycle of the application,
say 15-20 years, this will even out as costs for troubleshooting, maintenance,
multiple databases, and communications increase the long-term costs of PLCs. He
confesses that new process software is even helping industrial PCs find a niche
in mixed batch and discrete applications--especially where recipes and formulas
are involved in paints, baking, blending, mixing, batch control, recording,
reporting, and validating. This capability, he believes, is accelerating the
trend toward more open systems, industrial PCs, and truly distributed control
actually occurring in the field as opposed to a remote or centralized DCS
control room. He still maintains, however, that higher-level integration with
MES, ERP, and IT is easier done with a DCS than either a PLC or PC at this point
in their evolution.
"For many years, we have used Bailey Infi-90 DCSs
for process controls and motor starters," says Ben Fairweather, senior control
engineer at Appleton Coated Papers, Combined Locks, Wis. "And we still rely on
them quite heavily. Recently, however, we put in a DeltaV hybrid system for use
on our paper machines to do vacuum control, flow control, level, temperature
loops, and miscellaneous discrete functions such as valve on/off control. In
addition, we use PLCs for motor controls and other discrete applications. DeltaV
provides the HMI for the motors. Therefore, we leverage the OPC flexibility of
DeltaV to handle discrete PLC control as well."
According to process
systems supervisor Peter King, the Ultramar Golden Eagle refinery in Martinez,
Calif., has just about every type of control setup under the sun. "You name it
and we've got it," says King, "but mainly our plant depends on DCS for
continuous process controls--and a few PLCs for ancillary discrete service. We
even have a few old panel control boards that we are in the process of
replacing."
In addition to continuous control, the facility does a small
amount of batch control in blending various grades of gasoline. PLCs are used in
remote operation of valves, emergency shutdown systems, and miscellaneous skid
controls and emissions monitoring. PCs are scattered throughout the plant, but
used mainly for HMI and some gas turbine controls. "But the DCS is really
packaged to fit our particular applications--from hardware to software," says
King. "It's a strong legacy to overcome."
Marty Robbins, process control
engineering manager, Georgia-Pacific, Palatka, Fla., uses DCSs to regulate three
tissue and two kraft paper lines, 13 digesters, power recovery, and a water
treatment plant. "I have Foxboro I/A in power recovery and Honeywell TDC
2000/3000 for most all other processes, plus some Honeywell TotalPlant Solution
(TPS) nodes," says Robbins. Although Allen-Bradley PLCs are used for discrete
applications, some of those functions are handled by DCSs as well.
"I
guess you could say we are slowly migrating all of our process control functions
over to Foxboro I/A," says Robbins. In addition, the plant uses fully redundant
100 Mbit fiberoptic Ethernet for process communications. In the future, he plans
to add advanced control and model predictive control to the legacy systems.
Robbins says, "Not only will this help optimize our processes, but provide more
and better information to support production and maintenance management."
"Overall, I generally use a DCS in applications involving chemicals,
petroleum or petrochemicals, and other large-scale continuous processes," says
Dolan. "For discrete applications such as packaging, product transport, and
other standalone applications, I'll mix PLCs into the control equation. In
addition to the industries already mentioned, the metals industry will often use
a mini-VAX with PLCs for control. The plastics industry normally prefers its own
proprietary controls for such things as injection molding, extrusion, etc. This
may also take the form of PLCs and HMI. Plastics resin reactors, however,
normally use a DCS with triple modular redundancy because the processes are so
complex and difficult to re-start if anything goes wrong."
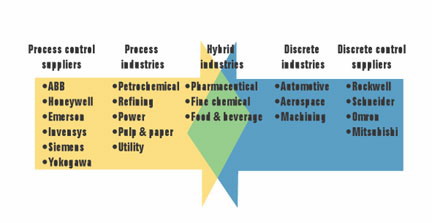 Figure 3: Control solutions
providers that began in the process or discrete worlds are converging on the
hybrid middle ground and are beginning to encroach on each other's home
turfs.
Hybrid Control: Emerging Solution Hybrid controllers
are crossing the lines between DCS and PLC solutions. Not coincidentally, they
are targeting the lucrative, fast-growing hybrid industries such as food and
beverage, pharmaceuticals, fine chemicals, and semiconductors. These hybrid
systems handle both process and discrete functions, and are well armed to
compete in the batch processing and supervisory control and data acquisition
(SCADA) markets.
Examples of these new hybrid control systems include
DeltaV from Fisher-Rosemount, PlantScape from Honeywell, the Micro I/A series
controller from Foxboro, Siemens Simatic PCS7, Rockwell ProcessLogix, and the
Centum CS 100 from Yokogawa (Figure 4). As expected, the market is divided into
two segments. One relies primarily on DCS for its process and discrete control
applications; the other mainly on PLCs with single and multiloop controllers for
process functions. Ideally, these control solutions are used in situations where
there is a mix of process field devices integrated with PLCs--or a combination
of PLCs and single and multiloop controllers.
ARCO Alaska, for example,
made headlines several years ago when it purchased a Fisher-Rosemount DeltaV
system to replace Siemens S5 PLCs. Other applications, such as a brewhouse, are
also digital I/O intensive, according to ARC, and require hybrid systems that
can handle large counts of digital I/O. Recently, hybrid control suppliers have
also added to their functional capabilities in enterprise level and supply chain
management. This has helped stimulate new market interest and growth.
"Ideally, a hybrid controller performs regulatory continuous process
(DCS) and discrete (PLC) control as well as batch and logic," says Paul
McLaughlin, director of PlantScape engineering, Honeywell Industrial Control,
Fort Washington, Pa. "The only real difference is in the algorithms that are
used." Hybrids can provide a DCS-grade infrastructure as well as a SCADA
infrastructure, and be used in process automation as well as discrete
automation.
"Automation functions will continue to consolidate as long
as suppliers seek to provide unified industrial solutions," says McLaughlin.
"That may result in cannibalizing some existing DCS and/or PLC business, but if
we don't do it, the competition will. We're in the business of providing
scalable, high-availability embedded control solutions, so we compete with both
DCS and PLC solutions--but not with PC control products."
Hybrid systems
are quite versatile. They can offer HMI/SCADA functionality, complex continuous
and discrete control, or demanding refinery and petrochemical functions; from
less than 10 up to 20,000 or 30,000 I/O. Hybrids also offer use of open,
interoperable bus technologies including Foundation fieldbus, AS-i bus, Profibus
DP, and DeviceNet. They often feature open standards such as OLE for Process
Control (OPC), XML, and ODBC. And they excel in integrating enterprise planning
systems with lower-level devices such as wireless phones, pagers, and PDAs.
Tom Shaw, automation manager at Cargill/Vitamin E in Eddyville, Iowa,
describes how his plant recently switched over from a combined DCS/PLC control
environment to a hybrid control system to achieve a common configuration
environment and a single integrated database. "Eliminating separate databases
for discrete and process control is a major operating advantage," says Shaw.
"Right now, the hybrid control system handles discrete, batch, and process
control--plus it interfaces to our legacy DCS system and provides a unified
database. Hybrid control simply meets all of our control and data needs. It's
safe to say that all of our future control requirements will migrate to hybrid
control as well."
Vernon Mills Textiles in Trion, Ga., is moving from a
System 3 DCS to a hybrid control system. "Most of our textile dye and finishing
operations are now controlled by a DeltaV hybrid controller," says process
control engineer Randy McDonald. "We are making the move due to lower installed
costs including smaller footprint, reduced installation and maintenance, fast
configuration, and the wealth of information available using Foundation fieldbus
and smart field devices. It is taking the place of a mix of 4-20 mA process and
discrete control solutions regulated mainly by the System 3 DCS.
"DeltaV
also offers us response times in the nanosecond range as compared to about a
half-second previously," he continues. "But what really sold us on the solution
was its ability to recover instantly after system shutdown or power failure.
There are no lengthy startup procedures, just normal checkout as everything
comes back up automatically. Previously, control functions were performed
differently by different operators. Now, everything is recipe-based and
virtually foolproof."
Gideon Richter Pharmaceuticals, Budapest, Hungary,
recently installed a PlantScape hybrid control system to integrate a reverse
osmosis (RO) water purification unit into its overall synthetic hormone
production facility. The objectives of the installation were to create automatic
batch reports, further develop and refine production technology, fulfill FDA
validation requirements, and identify and correct production deficiencies.
Specifically, the control system was implemented to reduce batch variances and
to minimize operator failures.
It also had to integrate additional
control elements without making major changes to existing facility hardware or
software. As a result, a single PlantScape controller was dedicated to handle
all of the data collection and control requirements of the RO water unit.
PlantScape's rotary station capability allows engineers to log onto the system
on their PCs to check data and monitor system performance. The familiar NT-based
operator interface also allows drag and drop configuration of I/O, continuous,
logic, motor, sequence, batch, and advanced control functions through a library
of function blocks.
Francisco Campa is head process development manager
at Dixie Group Carriage Industries, a textile dyeing plant in Calhoun, Ga. His
rationale for implementing a DeltaV hybrid control system is: "It does more than
just control. It organizes, manages, and communicates data while it also manages
multiple processes. We use it to control temperature, level, flow, and pressure,
and to interface with PLCs that regulate motors, on/off valves, and
miscellaneous discrete equipment. Thus, we have the highest level of confidence
in the data from these operations as they are fed quickly and accurately into a
corporate management system. Plus, it offers diagnostics and testing
capabilities that are not available with some PLC solutions."
PLCs:
Old Solution, New Twist As we have seen, even in the land of the process
giants, PLCs have played an important role in the many discrete control
functions that necessarily support most continuous process applications.
Mike La Rocca, senior process engineering specialist, Solutia Industrial
chemicals, Sauget, Ill., says his plant depends on DCS for continuous process
operation--about 75% of the applications are continuous process control. But 25%
are batch and discrete operations. For those (bagging, drumming, manufacture of
solid pastilles, and batch mixing), he depends on PLCs. "I feel in the not too
distant future it won't make any difference what controller you use, but how you
configure it, program it, and what software you use to execute the
functionality. We do a lot of batching, blending, and bagging in producing
chlorines, chlorobenzenes, and other additives used in the manufacture of animal
feeds, plastic bags, and wrappings. And most of that is controlled by PLCs."
The Climax Molybdenum Co. Mine and Mill in Parshall, Colo., uses a mix
of PLC, DCS, and SCADA. "Our controls are probably 60% PLC/HMI and 40% DCS,"
says Al Splettstosser, control systems coordinator. The facility uses PLCs with
HMI to control underground mining functions including water treatment, mine
ventilation, and more than 15 miles of conveyors. DCS is used to control mill
processes including cascade and ratio controllers to regulate loading, the mill
power drive, paper feeders, water controls, and grinding functions.
The
basic DCS system was installed in the early '80s mainly to control electric
power usage. It then spread to other functions such as water and wastewater,
pumping, and ventilation. In addition, Foxboro I/A is used to transfer
information from the PLCs to DCS. The only batch application is blending some of
the powdered reagent used in the processing. This is accomplished using PLCs.
"Because we use Allen-Bradley PLCs with HMI and historian software, we
might consider installing Rockwell's ProcessLogix to integrate our databases and
discrete and process controls in the future," says Splettstosser. "Until then,
DCS is our primary continuous process control solution. It provides the power
and applications we need without developing interfaces for incompatible products
with different protocols."
Just as hybrid controls based on DCS
technology are adding discrete control functionality, new PLCs are adding
process muscle to their discrete control capabilities. "ProcessLogix is simply
Rockwell's version of our PlantScape," says Honeywell's McLaughlin. "And its
ControlLogix is a next-generation PLC product that features discrete networking
via ControlNet. Furthermore, both can be applied as board-level products and
added to a controller to provide a wide range of solutions--both discrete and
process."
The Hexcel Corp. polymer plant in Decatur, Ala., recently
installed ProcessLogix on its polymer fiber line to optimize its mixing,
stretching, chemical treatment, and extrusion processes and increase overall
efficiency. The polymer line uses a mix of both batch and continuous process
control. "We needed efficiency without high dollar investment," says plant
engineer Jim Peppers. "ProcessLogix allows us to improve control and reduce
engineering and maintenance costs at the same time."
Since ProcessLogix
uses one common database for the server, controller, and operator interface, it
is inexpensive to install and maintain. It also offers drag-and-drop function
block programming, a library of process control functions, and a global
database. Plus, it offers the control functions normally found in traditional
DCS solutions.
Jeff Pierson, process engineer at BAE Systems Royal
Ordnance North America, Kingsport, Tenn., also uses a mix of PLC/HMI and DCS
solutions in the process of manufacturing high explosives. The facility's most
recent installation uses PCS7 controllers (PLCs) from Siemens, which perform
both discrete and process functions in the batch chemical manufacture of various
grades of explosives. There is also a Foxboro I/A DCS system that controls
distillation columns and related systems in the organic acids plant, and some
older Siemens and Allen-Bradley PLCs that control switches, valves, and pumps in
water, steam, and utility areas.
"In addition to the batch capability,
one of the reasons we chose PCS7 was because we already had PLC I/O in many of
these scattered production buildings," says Pierson. "We also needed the hot
backup capability provided by Siemens for our exothermic chemical reactions, and
wanted to use sequential function chart rather than ladder logic for programming
our applications."
"As PLCs and DCSs move toward each other
technologically, GE Fanuc continues to add functionality to its existing family
of products by offering process extensions or programming tools that can offer
truly integrated system solutions," says Lance Miller, open process manager for
GE Fanuc, Charlottesville, Va.
Open process solutions are giving
customers more functionality, ease of use, and the connectivity required for
scalable, integrated solutions. The city of Hazel Crest, Ill., needed a potable
water delivery system that could coordinate multiple remote pumping and metering
stations as well as control chemical treatment of the water. "Ideally, the
system should also integrate with a paging system to alert an on-call operator
of critical situations," says treatment plant engineer Jerry Davis. "It also had
to be affordable, flexible enough to meet changing requirements, and offer quick
return on investment."
The solution features GE Fanuc 90-30 PLCs and
Cimplicity HMI software, and provides communications through spread-spectrum
radio. Cimplicity HMI provides the graphics and alarming capability, as well as
standard historical evaluation tools. The solution has provided a return on
investment in less than two years. In addition, it generates daily reports for
environmental compliance, virtually eliminates manual data collection and device
control, and automatically logs system performance. "Best of all, it has cut
overtime in half," says Davis, "and we can even monitor system performance from
off site via phone."
PCs: Ready for Process? The market for
PC-based process control has grown remarkably during the last several years,
encroaching mainly on proprietary PLC applications, according to YeeYeen Wang,
national director for HMI and panel PCs, Advantech, Fremont, Calif. One must
realize, however, that PC-based control is starting from a much smaller market
share than PLC, DCS, and hybrid control solutions.
"Often, PCs are used
today to control machinery using remote I/O modules as a linkup," says Wang. At
higher levels of integration with MES, ERP, IT, and management databases, PCs
have an open systems advantage over both DCS and PLC solutions. "We find this
especially true in the food and beverage, water and wastewater, semiconductor,
and pharmaceutical industries. DCS and PLC solutions make sense in continuous
production of stable products in long-term markets. The inherent flexibility of
PC technology, however, better accommodates constantly fluctuating markets,
products, and services. And in the future, web connectivity for remote
monitoring and control is a major plus for users."
To allow for market
and technology changes, Advantech contracts stipulate that they will stock the
customer's necessary hardware and software for a specified period of time, or
provide a three to six-month advance notice of anticipated product or technology
changes. This provides customers with replacement products to maintain current
solutions, or an opportunity to plan an upgrade to the next level solution.
PC-based control made big news several years ago when Moscow-based AK
Transneft, one of the world's longest crude oil transmission systems, installed
300 networked PCs to provide supervisory control and data acquisition to its
pipeline network. The Windows-based PCs running Genesis HMI/SCADA from Iconics,
Foxborough, Mass., generated savings of more than three times that of
traditional UNIX and DCS systems, according to Victor Saenko, chief technical
officer. It monitors more than 187,000 digital and analog tags, and also
provides early warning of leak detection along the transmission system.
Since then, PC-based control has been used successfully in various
process applications, especially water and wastewater, pilot chemical and
pharmaceutical facilities, and food and beverage applications. Still, there are
reservations about using PCs in large-scale continuous processing plants.
"It is certainly feasible to use a PC to replace a DCS or PLC," says
Campa, "but not advisable for us at this point. If a PC is only collecting data
and crashes, the production process continues on regardless. But if it is
controlling the processes, shutdown and startup could be expensive--not to
mention possibly hazardous for machinery as well as humans."
"We use PCs
for SCADA and data collection--and even some non-critical control applications,"
says Cargill's Shaw, "but I'm not ready to trust my plant to a PC just yet for
reasons of safety, security, reliability, and mean time between failure."
"At Solutia Industrial Chemicals, it's against corporate guidelines to
allow a PC to control production processes," says La Rocca. "We deal with
hazardous chemicals and the safety issues are too great--plus consistent,
high-quality production is vital. There are just too many occurrences of PCs
locking up that require system shutdown and re-start."
Nalco Chemical
Co., however, operates a large pilot plant in Illinois whose function is process
development and scale-up to full production manufacturing. One of its processes
uses a reactor whose reactants are fed at multiple feed points using
positive-displacement pumps. To ensure accuracy, Nalco decided to integrate a
PC-based SCADA system to control the speed of the pumps through a feedback PID
loop. It used National Instruments Lookout HMI/SCADA software and Fieldpoint
distributed I/O to implement the application. All of the hardware was installed
in a NEMA 4 enclosure along with a Dell Pentium-based PC.
According to
Vivek Nayak, president of Vista Technology, a system integrator in Schaumburg,
Ill., the system was installed and commissioned with practically no operator
training. In addition, the PC-based system provided accurate, automated logging
of experimental data, easy data retrieval, and significantly increased the speed
and efficiency of the entire developmental research process.
Choices,
Choices, Choices In selecting the right process control solution, one can
no longer assume that a certain type or class of product is the right answer. As
technologies and control solutions merge, it is more important than ever to
judge on the basis of functionality, affordability, and overall lifecycle costs.
As we have seen, there is a considerable amount of discrete control even
in the large continuous process industries. Thus, the capability to perform
hybrid control functions will continue to be a moving force in the marketplace.
But what really is hybrid control, anyway? Is it the ability to function through
one unified control and management database? Is it the ability to do both
process and discrete control? Is it both control and database capabilities--or
those two plus something else? Even the suppliers and industry experts don't
agree on these points. Furthermore, what determines how efficiently and
effectively control is implemented? If everyone is trending toward the use of
the same (Intel) microprocessors, is it, as some would suggest, merely a matter
of software implementation?
Until such questions are answered thoroughly
and satisfactorily, it is more important than ever to carefully evaluate control
solution functionality. Kevin Stively, senior process controls engineer with the
engineering firm of Parker, Messana & Associates in Tacoma, Wash., attempted
to answer that question for the pulp and paper industry several years ago. He
began by postulating a theoretical application for a process unit that had 110
analog inputs, 68 analog outputs, 40 discrete (non-motor) inputs, 15 discrete
(non-motor) outputs, 50 motors with three discrete inputs (ready, running, and
overload), plus one output (run), and 24 PID loops.
His conclusion?
Large processes with more than 2,000 physical I/O points and a few hundred PID
loops might be best served by a traditional DCS. Smaller processes could
probably be controlled adequately by a mini-DCS, hybrid control system, or
PLC/HMI solution. The cost of these other solutions were about equal, and ran
44-48% less than that of a DCS. One of the most important criteria is that of
I/O selection and mix (analog, discrete, advanced process control, etc.).
But perhaps even more important than his conclusion is the methodology
used to evaluate control selection. He begins with a thorough analysis of the
process and its control needs, including types of control, I/O, and
communications interfaces. He then considers the strengths and weaknesses of the
various control platforms (DCS, PLC/HMI, mini-DCS, etc.). Design considerations
follow with an analysis of control architecture and where and how control should
be implemented (including scan times, system response, etc.). The inevitable
capital cost comparison (per I/O point or other reasonable comparison), is
followed by a benefits comparison based on both current and projected needs. A
review of various solution limitations is linked to configuration requirements.
And finally, training and service/maintenance considerations are discussed.
So there are no easy answers; simply lots of choices. Review them wisely
and carefully. For the time being, at least, functionality rules!
ICONICS Background Information
Founded in 1986, ICONICS is a leader in the
development of Web-enabled industrial automation and manufacturing intelligence
software for Microsoft® Windows® operating systems. Offering the industry's only
suite of fully-integrated OPC-based components and products, GENESIS32¢â
Enterprise Edition is available for Windows XP, 95, 98, Millennium, and 2000,
and Windows NT®. Pocket GENESIS¢â for Windows CE and Pocket PC was built from the
ground up based on ICONICS' OPC-To-The-Core¢â framework. BizViz¢â is a suite of
manufacturing and business intelligence products, which bridge the gap between
manufacturing and corporate business information systems. BizViz is designed
around Microsoft .NET technology, Microsoft SharePoint¢â and runs on Microsoft
server 2003. ICONICS also offers a complete set of Plug and Play automation
components, including best-in-class OPC ActiveX® Controls, OPC Toolkit, Human
Machine Interface (HMI), Microsoft SQL Server®–based data logging, Multimedia
Alarming, and Supervisory Control and Data Acquisition (SCADA) products. ICONICS
is a Microsoft Gold Certified partner, represented in over 50 countries and has
in excess of 150,000 products installations worldwide. For more information
contact ICONICS at (508) 543-8600 or visit us online at www.iconics.com.
© 2005 ICONICS, Inc. All rights reserved. GENESIS,
GENESIS32, Pocket GENESIS, Embedded GENESIS, GraphWorX, AlarmWorX, TrendWorX,
DataWorX, ProjectWorX, VCRWorX, TraceWorX, WebHMI, GenBroker, ControlWorX,
MachineWorX, ToolWorX, ToolBoX, BizViz, ReportWorX, BridgeWorX, PortalWorX,
MobileHMI, Visualize Your Enterprise, and OPC-To- The-Core are trademarks of
ICONICS Inc. Microsoft, Windows, ActiveX, Visual C++, Windows NT, and Visual
Basic are either registered trademarks or trademarks of Microsoft Corporation in
the United States and/or other countries. IBM and PC are trademarks of
International Business Machines Corp. Other product and company names mentioned
herein may be trademarks of their respective owners.
|
|
ÇöÀç ºÐ·ù¿¡ µî·ÏµÈ »óǰÀÌ ¾ø½À´Ï´Ù. |
|